Knowledge Base
Propeller Noise
Noise emitted by propulsion propellers remains an important factor onboard luxury Yachts. Important elements are:
- Number of blades
- Vertical clearance
- Type of propeller
- Cavitating or Non cavitating propeller
- Blade area
- Etc
Related to a displacement Yacht the first harmonic of the propeller blade frequency (in most of the cases) is below 50 Hz. For instance:
- Main Engine, maximum rpm is 2300 rpm
- Reduction ratio of the gearbox is 4 : 1
- Number of blades is 5.
Propeller blade frequency is equal to 2300 rpm / 60 / 4 = 9.5 Hz x 5 blades = 47.9 Hz.
The above shown frequency is equal to the first propeller blade frequency (first harmonic), a second up to a tenth harmonic (so 47.9 Hz up to 479 Hz) can occur pending on cavitation (see next chapter).
Achieving low pressure fluctuation levels, below 100 kg/m2, for a non cavitating propeller, is important to achieve low noise and vibration levels onboard. Important parameters are:
- Number of blades
- Vertical clearance
- Type of propeller
- Cavitating or Non cavitating propeller
In a second stage insulation materials can be used as shown below:
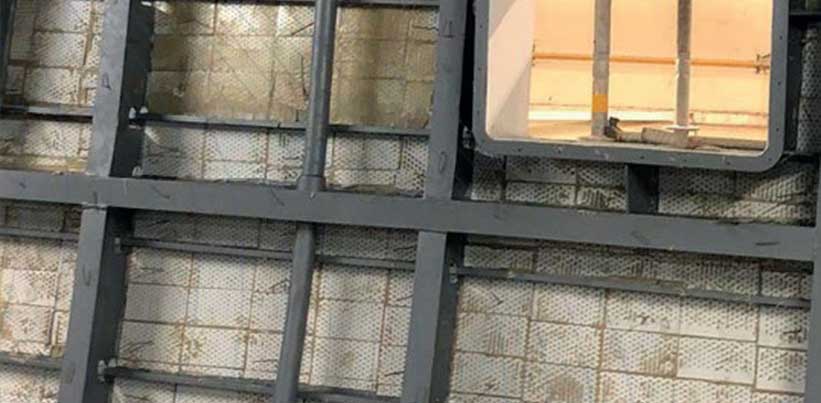
Steel structures
SLP – COMP (2 COMPONENT)
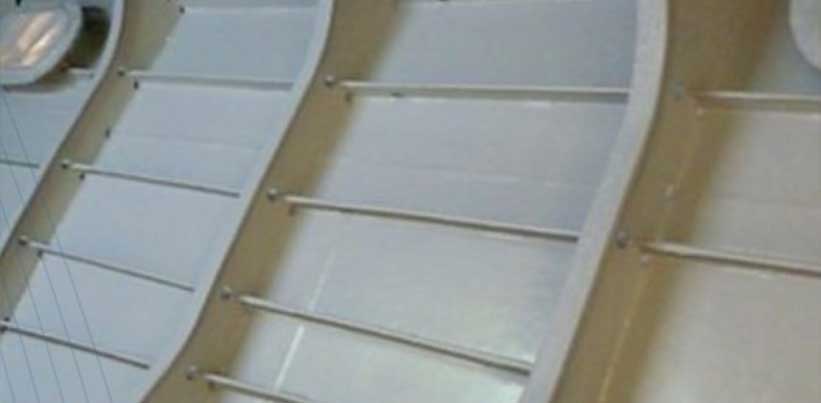
Aluminium structures
SLP – DAMP (1 COMPONENT)
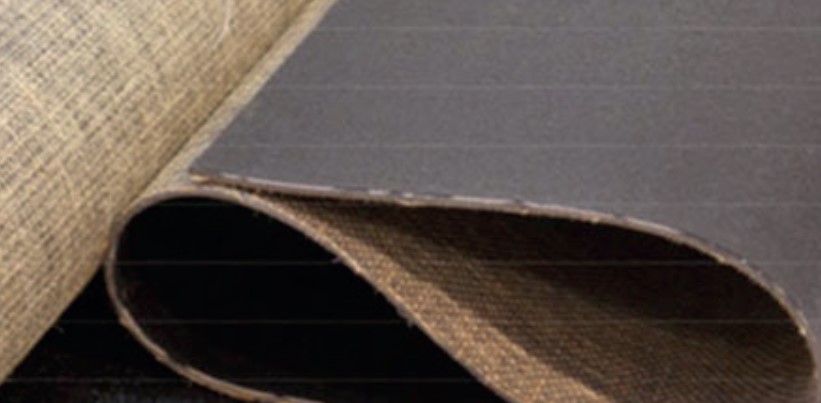
Fiberglass structures
SLP – MASS
For additional information on Silent Line Products (SLP) materials check www.silentlinegroup.com
Marine propeller cavitation
Cavitation can occur if an attempt is made to transmit too much power through the screw, or if the propeller is operating at a very high speed. Cavitation can occur in many ways on a propeller. The two most common types of propeller cavitation are suction side surface cavitation and tip vortex cavitation.
Suction side surface cavitation forms when the propeller is operating at high rotational speeds or under heavy load (high blade lift coefficient). The pressure on the upstream surface of the blade (the "suction side") can drop below the vapour pressure of the water, resulting in the formation of a pocket of vapour. Under such conditions, the change in pressure between the downstream surface of the blade (the "pressure side") and the suction side is limited, and eventually reduced as the extent of cavitation is increased. When most of the blade surface is covered by cavitation, the pressure difference between the pressure side and suction side of the blade drops considerably, and thrust produced by the propeller drops. This condition is called "thrust breakdown". This effect wastes energy, makes the propeller "noisy" as the vapour bubbles collapse, and most seriously, erodes the screw's surface due to localized shock waves against the blade surface
Tip vortex cavitation is caused by the extremely low pressures formed at the core of the tip vortex. The tip vortex is caused by fluid wrapping around the tip of the propeller; from the pressure side to the suction side. Tip vortex cavitation typically occurs before suction side surface cavitation and is less damaging to the blade, since this type of cavitation doesn't collapse on the blade, but some distance downstream.
Cavitation can be used as an advantage in design of very high performance propellers, in form of the supercavitating propeller. In this case, the blade section is designed such that the pressure side stays wetted while the suction side is completely covered by cavitation vapor. Because the suction side is covered with vapor instead of water it encounters very low viscous friction, making the supercavitating (SC) propeller comparably efficient at high speed. The shaping of SC blade sections however, make it inefficient at low speeds, when the suction side of the blade is wetted.
A similar, but quite separate issue, is ventilation, which occurs when a propeller operating near the surface draws air into the blades, causing a similar loss of power and shaft vibration, but without the related potential blade surface damage caused by cavitation. Both effects can be mitigated by increasing the submerged depth of the propeller: cavitation is reduced because the hydrostatic pressure increases the margin to the vapor pressure, and ventilation because it is further from surface waves and other air pockets that might be drawn into the slipstream.
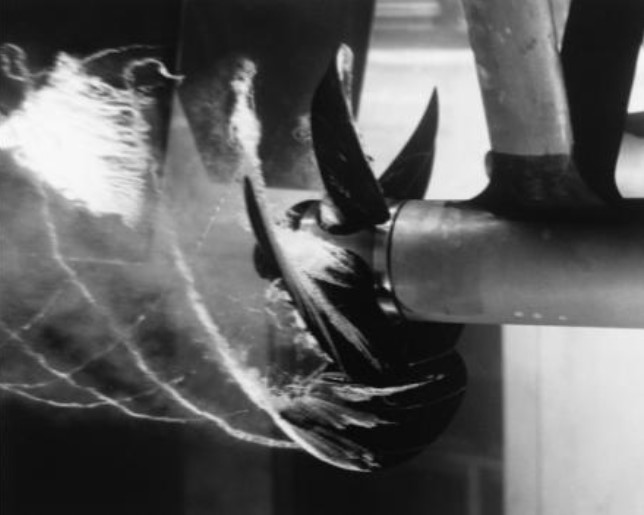